Фанера виготовляється з трьох або більше тонких шарів деревини, скріплених між собою клеєм. Кожен шар деревини, або фанери, зазвичай орієнтований так, щоб його волокна проходили під прямим кутом до сусіднього шару, щоб зменшити усадку та підвищити міцність готового виробу. Більшість фанери пресують у великі плоскі листи, які використовуються в будівництві будівель. Інші шматки фанери можуть бути сформовані у прості або складні криві для використання в меблях, човнах та літаках.
Використання тонких шарів деревини як засобу будівництва датується приблизно 1500 роком до нашої ери, коли єгипетські майстри склеювали тонкі шматки темного ебенового дерева до зовнішньої частини кедрової скриньки, знайденої в гробниці царя Тутанхамона. Пізніше цю техніку використовували греки та римляни для виготовлення вишуканих меблів та інших декоративних предметів. У 1600-х роках мистецтво декорування меблів тонкими шматками деревини стало відомим як фанерування, а самі вироби стали називатися шпоном.
До кінця 1700-х років шматки шпону вирізалися виключно вручну. У 1797 році англієць сер Семюел Бентам подав заявку на патенти, що охоплюють кілька машин для виробництва шпону. У своїх патентних заявках він описав концепцію ламінування кількох шарів шпону клеєм для утворення товстішого шматка — перший опис того, що ми зараз називаємо фанерою.
Незважаючи на цей розвиток, знадобилося ще майже сто років, перш ніж ламінований шпон знайшов якесь комерційне застосування поза меблевою промисловістю. Приблизно в 1890 році ламіновану деревину вперше почали використовувати для виготовлення дверей. Зі зростанням попиту кілька компаній почали виробляти листи багатошарової ламінованої деревини не лише для дверей, але й для використання у залізничних вагонах, автобусах та літаках. Незважаючи на це збільшення використання, концепція використання «клеєної деревини», як її саркастично називали деякі майстри, створила негативний імідж продукту. Щоб протидіяти цьому іміджу, виробники ламінованої деревини зустрілися та зрештою зупинилися на терміні «фанера» для опису нового матеріалу.
У 1928 році в Сполучених Штатах були представлені перші листи фанери стандартного розміру 4 фути на 8 футів (1,2 м на 2,4 м) для використання як загальний будівельний матеріал. У наступні десятиліття вдосконалені клеї та нові методи виробництва дозволили використовувати фанеру для широкого спектру застосувань. Сьогодні фанера замінила обрізану деревину для багатьох будівельних цілей, а виробництво фанери стало багатомільярдною галуззю світового масштабу.
Зовнішні шари фанери називаються відповідно лицьовою та зворотною сторонами. Лицьова сторона – це поверхня, яка використовується або бачиться, тоді як зворотна сторона залишається невикористаною або прихованою. Центральний шар називається серцевиною. У фанері з п'ятьма або більше шарами проміжні шари називаються поперечними смугами.
Фанера може бути виготовлена з твердих порід, м’яких порід або їх комбінації. Деякі поширені тверді породи включають ясен, клен, червоне дерево, дуб і тик. Найпоширенішою м’якою деревиною, що використовується для виготовлення фанери у Сполучених Штатах, є дугласія, хоча також використовуються кілька різновидів сосни, кедра, ялини та секвої.
Композитна фанера має серцевину, виготовлену з ДСП або шматків цільної деревини, з'єднаних краєм до краю. Лицьова та зворотна сторони її облицьовані шпоном фанери. Композитна фанера використовується там, де потрібні дуже товсті листи.
Тип клею, який використовується для склеювання шарів деревини разом, залежить від конкретного застосування готової фанери. Листи фанери з м'яких порід деревини, призначені для встановлення на зовнішній стороні конструкції, зазвичай використовують фенолформальдегідну смолу як клей завдяки її чудовій міцності та стійкості до вологи. Листи фанери з м'яких порід деревини, призначені для встановлення всередині конструкції, можуть використовувати клей на основі кров'яного білка або соєвого білка, хоча більшість листів м'якої деревини для внутрішнього оздоблення зараз виготовляються з тієї ж фенолформальдегідної смоли, що й для зовнішніх листів. Фанера з твердих порід деревини, яка використовується для внутрішнього оздоблення та у виробництві меблів, зазвичай виготовляється з сечовиноформальдегідної смоли.
У деяких випадках потрібні листи фанери, які мають тонкий шар пластику, металу або просоченого смолою паперу чи тканини, склеєний з лицьової або зворотної сторони (або обох), щоб надати зовнішній поверхні додаткової стійкості до вологи та стирання або покращити її властивості утримання фарби. Така фанера називається накладною фанерою і зазвичай використовується в будівництві, транспорті та сільському господарстві.
Інші листи фанери можуть бути покриті рідкою морилкою, щоб надати поверхням завершеного вигляду, або можуть бути оброблені різними хімічними речовинами для покращення вогнестійкості фанери або стійкості до гниття.
Існує два широких класи фанери, кожен з яких має власну систему класифікації.
Один клас відомий як будівельний та промисловий. Фанера цього класу використовується в основному завдяки своїй міцності та оцінюється за здатністю до впливу навколишнього середовища та сортом шпону, що використовується на лицьовій та зворотній сторонах. Здатність до впливу навколишнього середовища може бути внутрішньою або зовнішньою, залежно від типу клею. Сорти шпону можуть бути N, A, B, C або D. Сорти N мають дуже мало поверхневих дефектів, тоді як сорт D може мати численні сучки та тріщини. Наприклад, фанера, яка використовується для чорнової підлоги в будинку, має рейтинг "Внутрішня CD". Це означає, що вона має лицьову сторону C та зворотну сторону D, і клей підходить для використання в захищених місцях. Внутрішні шари всієї будівельної та промислової фанери виготовляються зі шпону сорту C або D, незалежно від рейтингу.
Інший клас фанери відомий як листяна та декоративна. Фанера цього класу використовується переважно завдяки своєму зовнішньому вигляду та класифікується у порядку спадання стійкості до вологи як технічна (зовнішня), тип I (зовнішня), тип II (внутрішня) та тип III (внутрішня). Їхні лицьові шпони практично не мають дефектів.
Розміри
Товщина листів фанери коливається від 1,6 мм (0,06 дюйма) до 76 мм (3,0 дюйма). Найпоширеніша товщина становить від 6,4 мм (0,25 дюйма) до 19,0 мм (0,75 дюйма). Хоча серцевина, поперечні смуги, а також лицьова та задня сторони листа фанери можуть бути виготовлені з шпону різної товщини, товщина кожного з них повинна бути збалансована навколо центру. Наприклад, лицьова та задня сторони повинні бути однакової товщини. Аналогічно, верхня та нижня поперечні смуги повинні бути однаковими.
Найпоширеніший розмір листів фанери, що використовуються в будівництві, становить 1,2 м завширшки та 2,4 м завдовжки. Інші поширені розміри ширини – 0,9 м та 1,5 м. Довжина варіюється від 2,4 м до 3,6 м з кроком 0,3 м. Для спеціальних застосувань, таких як будівництво човнів, можуть знадобитися листи більшого розміру.
Дерева, що використовуються для виготовлення фанери, зазвичай меншого діаметра, ніж ті, що використовуються для виготовлення пиломатеріалів. У більшості випадків їх посадили та вирощують на ділянках, що належать фанерній компанії. Ці ділянки ретельно обробляються, щоб максимізувати ріст дерев та мінімізувати пошкодження від комах або вогню.
Ось типова послідовність операцій для обробки дерев у стандартні листи фанери розміром 4 фути на 8 футів (1,2 м на 2,4 м):
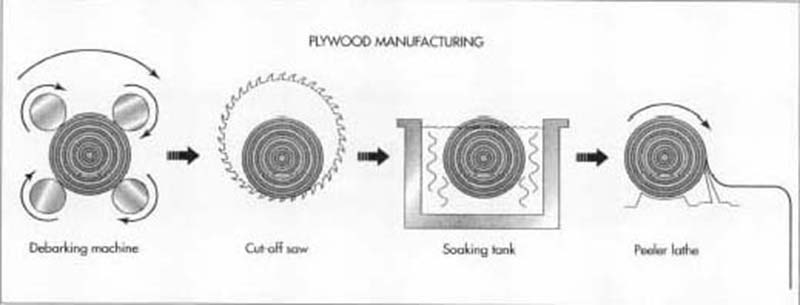
Колоди спочатку очищають від кори, а потім розрізають на бруски для лущення. Щоб нарізати бруски на смужки шпону, їх спочатку замочують, а потім лущать на смужки.
1 Вибрані дерева на певній ділянці позначаються як готові до зрубування або валки. Валку можна виконувати за допомогою бензопил або великих гідравлічних ножиць, встановлених на передній частині колісних транспортних засобів, які називаються вальцями. Гілки видаляються з повалених дерев за допомогою бензопил.
2 Обрізані стовбури дерев, або колоди, перевозять до місця навантаження колісними транспортними засобами, які називаються трелювальними тракторами. Колоди розрізають на потрібну довжину та вантажать у вантажівки для транспортування на фанерний завод, де їх складають у довгі штабелі, відомі як колоди.
3 Коли колоди потрібні, їх піднімають з колод за допомогою гумових навантажувачів і розміщують на ланцюговому конвеєрі, який доставляє їх до короочисної машини. Ця машина видаляє кору або за допомогою гострозубих шліфувальних кругів, або за допомогою струменів води під високим тиском, поки колода повільно обертається навколо своєї поздовжньої осі.
4 Очищені від кори колоди транспортуються на млин ланцюговим конвеєром, де величезна дискова пилка розрізає їх на секції довжиною приблизно від 2,5 м до 2,6 м, придатні для виготовлення стандартних листів довжиною 2,4 м. Ці секції колод відомі як лущильні блоки.
5 Перш ніж різати шпон, блоки для лущення необхідно нагріти та замочити, щоб розм’якшити деревину. Блоки можна обробляти парою або занурювати в гарячу воду. Цей процес триває від 12 до 40 годин залежно від типу деревини, діаметра блоку та інших факторів.
6 Нагріті блоки шпону потім транспортуються до токарного верстата, де вони автоматично вирівнюються та подаються в токарний верстат по одному. Коли токарний верстат швидко обертає блок навколо своєї поздовжньої осі, лезо ножа повної довжини відшаровує безперервний лист шпону з поверхні обертового блоку зі швидкістю 90-240 м/хв. Коли діаметр блоку зменшується приблизно до 230-305 мм, шматок деревини, що залишився, відомий як серцевина шпону, викидається з токарного верстата, а на його місце подається новий блок шпону.
7 Довгий лист шпону, що виходить з токарного верстата з лущенням, може бути оброблений негайно, або його можна зберігати в довгих багаторівневих лотках або намотувати на рулони. У будь-якому випадку, наступний процес включає розрізання шпону на частини корисної ширини, зазвичай близько 1,4 м (4 фути-6 дюймів), для виготовлення стандартних листів фанери шириною 1,2 м (4 фути). Водночас оптичні сканери шукають ділянки з неприйнятними дефектами, і вони вирізаються, залишаючи шматки шпону меншої за стандартну ширину.
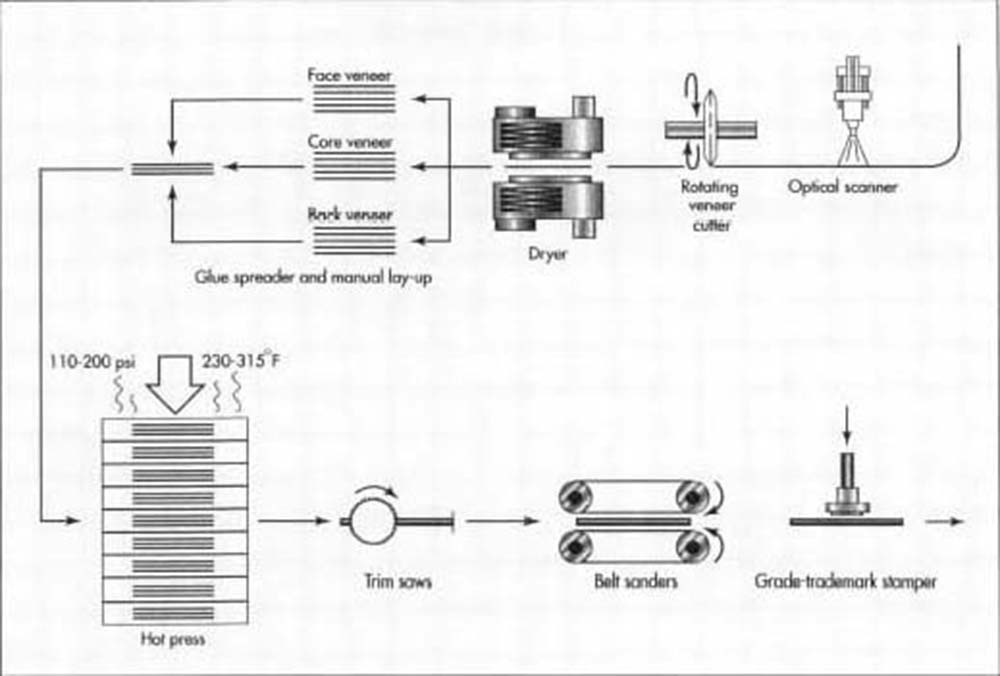
Вологі смужки шпону змотуються в рулон, а оптичний сканер виявляє будь-які неприйнятні дефекти деревини. Після висихання шпон сортується та складається в штабель. Вибрані ділянки шпону склеюються разом. Гарячий прес використовується для герметизації шпону в один суцільний шматок фанери, який потім обрізається та шліфується, перш ніж на нього наноситься штамп відповідного сорту.
8 Потім секції шпону сортуються та складаються за ґатунком. Це може бути зроблено вручну або автоматично за допомогою оптичних сканерів.
9 Відсортовані секції подаються в сушарку, щоб зменшити їх вміст вологи та дати їм усадку перед склеюванням. Більшість фанерних заводів використовують механічну сушарку, в якій деталі безперервно рухаються через нагріту камеру. У деяких сушарках струмені високошвидкісного нагрітого повітря продуваються по поверхні деталей, щоб пришвидшити процес сушіння.
10 Коли секції шпону виходять із сушарки, їх складають відповідно до сорту. Секції з меншою шириною мають додатковий шпон, зрощений стрічкою або клеєм, щоб зробити деталі придатними для використання у внутрішніх шарах, де зовнішній вигляд та міцність менш важливі.
11 Ті секції шпону, які будуть встановлені поперек — серцевина в тришарових листах або поперечні смуги в п'ятишарових листах — нарізаються на шматки довжиною приблизно 1,3 м (4 фути 3 дюйми).
12 Коли відповідні секції шпону зібрані для певного ряду фанери, починається процес укладання та склеювання деталей. Це може бути зроблено вручну або напівавтоматично за допомогою машин. У найпростішому випадку тришарових листів задній шпон укладається плоско та пропускається через клеєрозподільник, який наносить шар клею на верхню поверхню. Потім короткі секції серцевинного шпону укладаються поперек поверх склеєної задньої частини, і весь лист вдруге пропускається через клеєрозподільник. Нарешті, лицьовий шпон укладається поверх склеєної серцевини, і лист складається з іншими листами, які очікують на потрапляння до преса.
13 Склеєні листи завантажуються в гарячий прес з кількома отворами. Преси можуть обробляти 20-40 листів одночасно, причому кожен лист завантажується в окремий отвір. Коли всі листи завантажено, прес стискає їх разом під тиском приблизно 110-200 psi (7,6-13,8 бар), одночасно нагріваючи їх до температури приблизно 230-315° F (109,9-157,2° C). Тиск забезпечує хороший контакт між шарами шпону, а тепло призводить до належного затвердіння клею для досягнення максимальної міцності. Через 2-7 хвилин прес відкривається, і листи вивантажуються.
14 Потім чорнові листи проходять через набір пилок, які обрізають їх до кінцевої ширини та довжини. Листи вищого ґатунку проходять через набір стрічкових шліфувальних машин шириною 1,2 м, які шліфують як лицьову, так і зворотну сторони. Листи середнього ґатунку шліфуються вручну точечно для очищення шорстких ділянок. Деякі листи пропускаються через набір дискових пил, які вирізають неглибокі пази на лицьовій стороні, щоб надати фанері текстурованого вигляду. Після остаточної перевірки всі дефекти, що залишилися, ремонтуються.
15 Готові аркуші штампуються торговою маркою класу, яка надає покупцеві інформацію про ступінь впливу, клас, номер заводу та інші фактори. Аркуші одного й того ж класу та торгової марки зв'язуються стопками та переміщуються на склад для очікування відвантаження.
Як і у випадку з пиломатеріалами, не існує ідеального шматка фанери. Усі шматки фанери мають певну кількість дефектів. Кількість і розташування цих дефектів визначають сорт фанери. Стандарти для будівельної та промислової фанери визначені Стандартом на продукцію PS1, підготовленим Національним бюро стандартів та Американською асоціацією фанери. Стандарти для фанери з твердих порід деревини та декоративної фанери визначені ANSIIHPMA HP, підготовленим Американським національним інститутом стандартів та Асоціацією виробників фанери з твердих порід деревини. Ці стандарти не лише встановлюють системи класифікації фанери, але й визначають критерії конструкції, експлуатаційних характеристик та застосування.
Навіть попри те, що фанера досить ефективно використовує дерева — по суті, розбираючи їх на частини та збираючи знову в міцнішу, зручнішу конфігурацію — у виробничому процесі все ще утворюється значна кількість відходів. У більшості випадків лише близько 50-75% корисного об'єму деревини перетворюється на фанеру. Щоб покращити цей показник, розробляється кілька нових продуктів.
Один новий продукт називається орієнтовано-стружкова плита, яку виготовляють шляхом подрібнення всієї колоди на стружки, а не шляхом відшаровування шпону від колоди та викидання серцевини. Стружки змішують з клеєм і пресують у шари з волокнами, спрямованими в одному напрямку. Ці стиснуті шари потім орієнтують під прямим кутом один до одного, як фанера, і склеюють між собою. Орієнтовано-стружкова плита така ж міцна, як фанера, і коштує трохи менше.
Час публікації: 10 серпня 2021 р.